How Do Manufacturers Determine the Right Compression Spring Design?
Compression springs are widely used in various industries, from automotive to aerospace and medical devices.
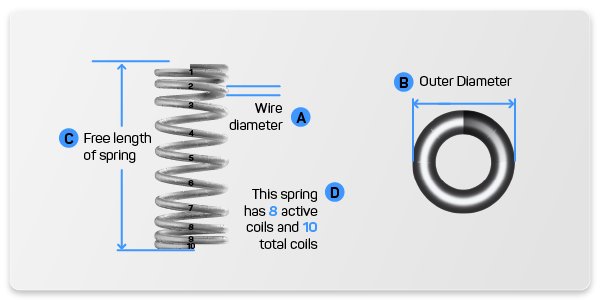
Compression springs are widely used in various industries, from automotive to aerospace and medical devices. Manufacturers must carefully design these springs to ensure they meet specific load-bearing and performance requirements. The process of determining the right compression spring design involves precise calculations, material selection, and adherence to industry standards. One critical aspect of this design process is using the spring rate formula, which helps engineers ensure the spring performs as expected.
Understanding Compression Spring Design
Compression springs function by absorbing and storing mechanical energy when compressed. They return to their original shape when the applied force is removed. To achieve optimal performance, compression spring manufacturers consider several factors, including material type, wire diameter, coil count, and end types.
Factors Affecting Compression Spring Design
1. Load and Deflection Requirements
The most crucial factor in spring design is understanding the load and deflection requirements. Manufacturers must determine how much force the spring must withstand and how far it needs to compress under that force. This helps in calculating the spring rate.
2. Spring Rate Formula
The spring rate formula plays a vital role in compression spring design. The spring rate (k) is the amount of force required to compress the spring by one unit of length. It is calculated using the following formula:
Where:
- k = Spring rate (force per unit of deflection)
- G = Modulus of rigidity of the material
- d = Wire diameter
- D = Mean coil diameter
- N = Number of active coils
This formula allows engineers to adjust parameters to achieve the desired spring stiffness and performance.
3. Material Selection
The choice of material significantly impacts the durability and performance of compression springs. Some commonly used materials include:
- Music Wire – High tensile strength, ideal for general applications.
- Stainless Steel – Corrosion-resistant, suitable for medical and marine environments.
- Phosphor Bronze – Excellent electrical conductivity, used in electronic applications.
- Inconel – High-temperature resistance, preferred for aerospace and industrial applications.
4. Wire Diameter and Coil Count
The wire diameter and the number of coils influence the overall spring rate. A thicker wire increases the stiffness, while a higher number of coils generally results in a softer spring. Adjusting these variables helps fine-tune the spring’s performance.
5. End Types and Finishing
Compression springs can have different end configurations, such as:
- Closed and Ground Ends – Provide stability and uniform load distribution.
- Closed and Squared Ends – Offer better alignment and reduce tangling.
- Open Ends – Less common but used in specific applications where flexibility is needed.
Manufacturers also apply surface treatments like plating, powder coating, or shot peening to enhance durability and corrosion resistance.
The Manufacturing Process of Compression Springs
1. Design and Prototyping
Once manufacturers determine the spring specifications using the spring rate formula, they create digital models using CAD software. Prototypes are then produced and tested to ensure they meet performance criteria.
2. Coiling and Forming
The selected material is wound into the desired coil shape using CNC coiling machines. Precision is crucial to maintaining consistency across batches.
3. Heat Treatment
After coiling, springs undergo heat treatment to relieve internal stresses and enhance durability. This process improves the spring’s ability to withstand repeated compression cycles.
4. Finishing and Quality Control
Springs are often coated or plated to improve corrosion resistance. Manufacturers conduct rigorous testing, including:
- Load testing to verify force-deflection characteristics
- Fatigue testing to assess long-term performance
- Dimensional checks for precision
Importance of Working with Experienced Compression Spring Manufacturers
Choosing the right compression spring manufacturers is essential for ensuring quality and performance. Experienced manufacturers offer:
- Custom Spring Design – Tailored solutions to meet specific application needs.
- Precision Engineering – Advanced technology for high accuracy.
- Compliance with Standards – Adherence to industry regulations like ASTM and ISO.
- Material Expertise – Guidance on selecting the best material for durability and functionality.
Conclusion
Determining the right compression spring design requires careful consideration of load requirements, material selection, and adherence to the spring rate formula. By working with reputable compression spring manufacturers, businesses can ensure they receive high-quality springs optimized for their specific applications. Proper design and testing guarantee reliability, efficiency, and longevity in various industrial uses.
What's Your Reaction?






